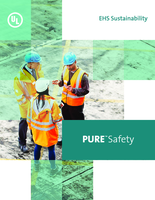
PURE Safety Brochure
Software solutions customized for safety, learning, sustainability, and occupational health management. Designed for businesses that want to protect their employees, manage their operational risks, manage OSHA compliance and optimize day-to-day performance.
Safety management software helps ensure compliance, manage incidents and minimize operational risk. You can log your incidents, assign corrective actions, analyze underlying causes and report on incident rates all in one central location.
Manage performance across all areas of your sustainability program. Transform the way you gather complex data by streamlining the data collection process and provide automated reporting for your annual CR or sustainability reports.
Select from hundreds of courses from our library of engaging and up-to-date content or customize existing courses to meet your unique environment, health and safety (EHS) learning objectives. From workplace safety to incident management and prevention, all of our courses are measurable for participation tracking. If you need a course that doesn’t yet exist, we’ll work with you to create it.
Our compliance solutions help life science organizations drive results in compliance, quality and organizational performance, so they can enter new markets, stay in those markets and grow.
A suite of tools and modules to manage your organization’s health and wellness programs and increase productivity. This includes powerful tools, such as medical compliance management, health management of your workforce and workflow automation for recording clinic visits or billing.
"We use the PURE platform from UL to collect supply chain, environmental and employee data from 18 subsidiaries and more than 700 sites. The system gives us a detailed overview of ethical and environmental data from our supply chains."
As an IACET Accredited Provider, UL Solutions’ EHS Sustainability team offers IACET CEUs for its learning events that comply with the ANSI/IACET Continuing Education and Training Standard.
Thanks for your interest in our products and services. Let's collect some information so we can connect you with the right person.